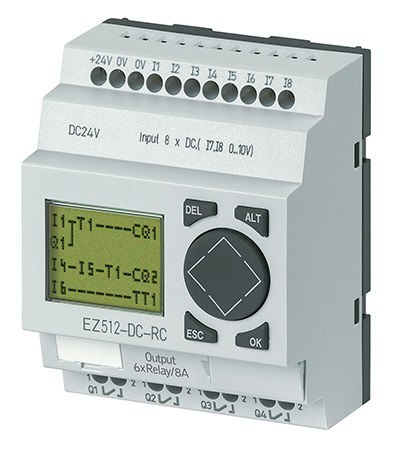
Programmable Logic Controllers (PLCs) are widely used in various industries for automation and control purposes. These devices rely on relays to interface with external devices and perform switching operations. However, not all relays are suitable for PLC applications. In this article, we will delve into the different types of relays used in PLCs and explore the factors to consider when selecting the optimal relay for a specific application.
- Electromechanical Relays:
Electromechanical relays are commonly used in PLCs due to their reliability and versatility. These relays consist of a coil and a set of contacts that open or close when the coil is energized. They can handle both AC and DC voltages, making them suitable for a wide range of applications. However, they have mechanical components that can wear out over time, leading to potential maintenance issues. - Solid-State Relays (SSRs):
SSRs have gained popularity in recent years due to their numerous advantages over electromechanical relays. These relays use semiconductor devices, such as thyristors or triacs, to perform the switching operation. SSRs offer faster switching speeds, longer lifespan, and better resistance to shock and vibration. They also eliminate the need for mechanical contacts, reducing the risk of arcing and improving reliability. However, SSRs may have higher initial costs and limited current-carrying capabilities compared to electromechanical relays. - Reed Relays:
Reed relays are another type of relay commonly used in PLC applications. They consist of a pair of magnetic contacts enclosed in a glass tube. When a magnetic field is applied, the contacts close, allowing current to flow. Reed relays offer fast switching speeds, low power consumption, and excellent isolation between the control and load circuits. However, they are more susceptible to damage from overvoltage or high currents, making them less suitable for high-power applications. - Hybrid Relays:
Hybrid relays combine the advantages of electromechanical and solid-state relays. They utilize a small electromechanical relay to control a larger solid-state relay. This configuration allows for efficient switching of high currents while maintaining the reliability of the electromechanical relay. Hybrid relays are often used in PLC applications that require both high power handling and fast switching speeds.
Factors to Consider when Selecting a Relay for PLC Applications:
- Current and voltage requirements: Ensure the selected relay can handle the expected current and voltage levels of the application.
- Switching speed: Consider the required response time and choose a relay with an appropriate switching speed.
- Environmental conditions: Evaluate the operating environment for factors such as temperature, humidity, and vibration, and select a relay that can withstand these conditions.
- Reliability and lifespan: Assess the expected lifespan and reliability requirements of the application and choose a relay accordingly.
- Cost: Consider the initial cost and long-term maintenance costs of the relay.
Conclusion:
Selecting the right relay for PLC applications is crucial for ensuring reliable and efficient operation. Electromechanical relays, solid-state relays, reed relays, and hybrid relays each have their advantages and considerations. By carefully evaluating the specific requirements of the application and considering factors such as current and voltage requirements, switching speed, environmental conditions, reliability, and cost, engineers can make informed decisions to optimize their PLC systems.