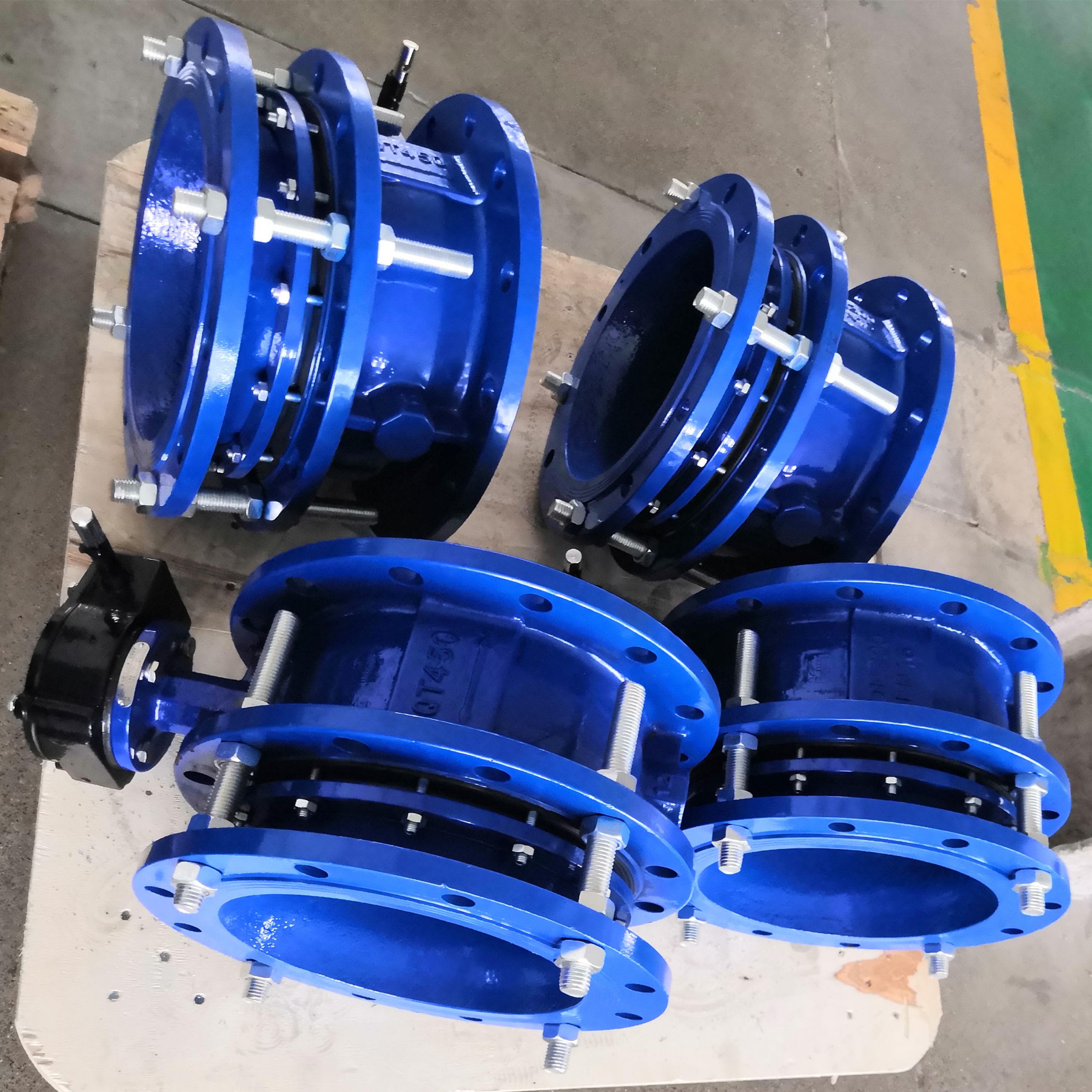
Mechanical joints play a pivotal role in various industries, serving as the foundation for connecting different components and enabling the seamless operation of machinery and structures. Understanding what is considered a mechanical joint is crucial for engineers, designers, and professionals across multiple disciplines. In this comprehensive blog post, we will delve into the intricacies of mechanical joints, exploring their types, applications, and the factors that contribute to their effectiveness and reliability.
- The Definition and Purpose of Mechanical Joints:
Mechanical joints are structural elements designed to connect two or more components, allowing for motion, load transmission, and assembly. These joints are essential in achieving stability, strength, and functionality in a wide range of applications, including automotive, aerospace, construction, and manufacturing industries. By understanding the different types of mechanical joints, engineers can select the most suitable option for their specific requirements. - Types of Mechanical Joints:
2.1. Permanent Joints:
- Welded Joints: Welding is a common method of permanently joining two or more components by melting and fusing them together. This type of joint offers excellent strength and durability, making it ideal for heavy-duty applications.
- Adhesive Joints: Adhesives are used to bond components together, providing a strong and reliable connection. This type of joint offers advantages such as weight reduction, improved aesthetics, and stress distribution.
2.2. Semi-Permanent Joints:
- Bolted Joints: Bolted joints utilize threaded fasteners, such as screws and bolts, to secure components together. This type of joint allows for disassembly and reassembly, making it suitable for applications that require maintenance or adjustments.
- Riveted Joints: Rivets are used to permanently join components by deforming and securing them together. This type of joint offers high strength and resistance to vibration, making it commonly used in structural applications.
2.3. Temporary Joints:
- Snap-fit Joints: Snap-fit joints rely on interlocking features to connect components without the need for additional fasteners. This type of joint offers quick assembly and disassembly, making it popular in consumer products and assembly lines.
- Press-fit Joints: Press-fit joints involve inserting one component into another with an interference fit, creating a secure connection without the need for additional fasteners. This type of joint is widely used in the assembly of shafts, bearings, and gears.
- Factors Influencing Joint Design and Performance:
3.1. Load and Stress Distribution: The type and magnitude of the applied load significantly impact joint design. Engineers must consider factors such as tension, compression, shear, and torsion to ensure the joint can withstand the expected forces and distribute them effectively.
3.2. Material Compatibility: The compatibility of materials used in the joint is crucial for achieving a reliable connection. Factors such as thermal expansion, corrosion resistance, and mechanical properties must be considered to prevent premature joint failure.
3.3. Environmental Conditions: The operating environment, including temperature, humidity, and exposure to chemicals or vibrations, can affect the performance and longevity of mechanical joints. Proper selection of materials and protective coatings is essential to ensure durability.
3.4. Manufacturing and Assembly Considerations: Joint design should take into account the ease of manufacturing and assembly processes. Factors such as accessibility, tooling requirements, and tolerances play a vital role in achieving efficient and cost-effective joint production.
Conclusion:
Mechanical joints are the backbone of countless industries, enabling the seamless integration and operation of various components. By understanding the different types of mechanical joints, their applications, and the factors influencing their design and performance, engineers and professionals can make informed decisions to ensure reliable and efficient connections. Whether it's welding, bolting, or snap-fitting, each type of joint has its unique advantages and considerations. By harnessing the power of mechanical joints, we can continue to push the boundaries of innovation and build a more connected world.