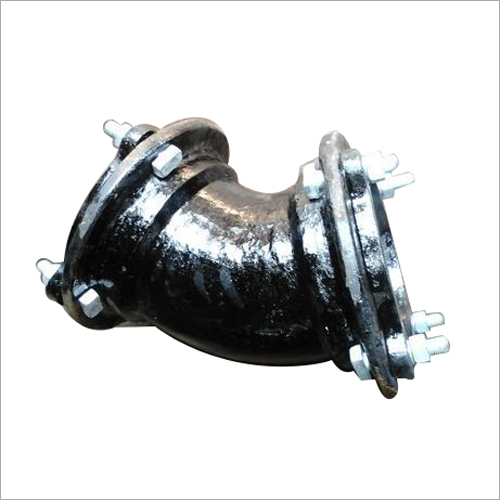
Mechanical joints play a crucial role in various industries, providing the necessary connections for structural integrity and functionality. However, a fundamental question arises: Are all mechanical joints truly restrained? In this comprehensive blog post, we will delve into the intricacies of mechanical joints, examining the factors that determine their restraint and exploring the implications for different applications. By shedding light on this topic, we aim to provide valuable insights for engineers, designers, and enthusiasts alike.
- Understanding Mechanical Joints:
Mechanical joints encompass a wide range of connection methods, including bolts, welds, rivets, and adhesives. These joints are designed to transmit loads, resist movement, and maintain stability in assembled structures. However, the level of restraint exhibited by a joint depends on several key factors. - Factors Influencing Joint Restraint:
a. Material Properties: The mechanical properties of the joint materials, such as stiffness and ductility, significantly impact the joint's restraint. Higher stiffness materials tend to exhibit greater restraint, while ductile materials may allow for more flexibility.
b. Geometric Design: The joint's geometry, including the shape, size, and contact area, affects its restraint. Complex geometries with increased contact surfaces often result in enhanced joint stability.
c. Preload and Torque: The application of preload or torque during joint assembly can influence the level of restraint. Properly controlled preload or torque can enhance joint performance and minimize the risk of loosening or failure. - Types of Restraint in Mechanical Joints:
a. Rigid Restraint: Some mechanical joints, such as fully welded connections, provide rigid restraint, preventing any relative movement between the connected parts. These joints offer excellent load transfer and structural stability.
b. Partial Restraint: Many mechanical joints exhibit partial restraint, allowing limited movement or rotation under certain loads. Bolted connections with a specified torque, for example, provide controlled flexibility while maintaining sufficient stability.
c. Non-Restraint: In certain applications, mechanical joints may intentionally allow for unrestricted movement. This is commonly observed in expansion joints, which accommodate thermal expansion and contraction in structures. - Restraint Considerations for Different Applications:
a. Structural Engineering: In the design of buildings, bridges, and other large-scale structures, understanding joint restraint is crucial for ensuring overall stability and load distribution. Proper analysis and selection of joint types are essential to meet safety requirements.
b. Automotive Industry: Mechanical joints in automobiles must withstand dynamic loads, vibrations, and environmental factors. Balancing restraint and flexibility is vital to ensure longevity and performance.
c. Aerospace and Defense: Joints in aircraft and defense systems demand high levels of restraint to withstand extreme conditions and maintain structural integrity. Advanced joint designs and materials are employed to achieve optimal performance.
Conclusion:
In conclusion, not all mechanical joints are equally restrained. The level of restraint depends on various factors, including material properties, geometric design, and applied preload or torque. Understanding the restraint characteristics of different joints is crucial for engineers and designers in various industries. By considering the specific requirements of each application, appropriate joint types can be selected to achieve the desired balance between stability and flexibility. As technology advances, further research and innovation in mechanical joint design will continue to enhance the performance and reliability of structures and systems across industries.